画期的なコンセプトを、具体的な形に示して"ものづくり"の夢を実現する
将来にわたって、徹底的に差別化できる、オリンパスにしかないマシンを作ろう!こうした強い思いが、複雑形状部品を段取りゼロで、高速1個加工できるマシンの自社開発を加速しました。
ここには、画期的なコンセプト提案、そのコンセプトの具体化、地道に積み上げてきた「加工技術・技能ノウハウ」を盛り込んで"ものづくり"を実現するという、将来の金属加工の夢を描いた行動がみごとに結実しています。
世の中に存在しない、画期的なコンセプトを提案する
内視鏡を構成する部品は、ごく限られたスペースの中で多くの機能を果たすために、極めて精密で複雑な形状をしている部品が多くあります。また、その材料も耐薬品性が高いことからステンレス系の難切削材が多く使われています。
内視鏡の金属部品加工は、換言すると「複雑形状難切削材の加工」です。どれぐらい形状が複雑であるかは、ちょっと図面を見ただけではイメージできません。オリンパスの金属加工は、このような内視鏡の部品加工に挑むことで発展してきました。
1998(平成10)年、生産技術本部(現・ものづくり革新センター)において、それまで取り組んできたさまざまな金属加工機・加工法を振り返り、将来、金属加工はどういう方向に進むのか討議を行いました。生産技術本部の加工法開発者、設備開発者、電気技術者、IE技術者等が結集したこの場では、いろいろな視点から未来の金属加工機の姿が論じられました。
このときにまとめられた加工機のコンセプトは、当時の世の中の工作機械にないものでした。簡単に言うと、材料を投入したなら、どんな複雑形状であっても高精度の部品が1個、ポロッと最速で出てくるというイメージです。
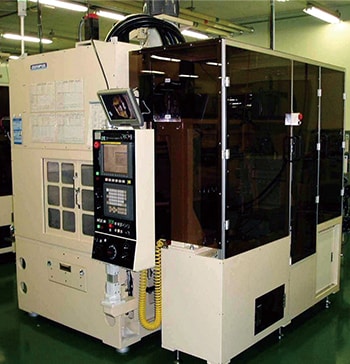
オリンパス独自の開発による複合加工機。複雑形状部品を段取りゼロで、高速1個加工できる。
具体的には、3次元的に複雑形状の部品を高精度(数マイクロメートルの公差)かつ高速で加工し、かつ段取り時間はゼロ、寸法補正も加工機の中で行います。もちろん5軸+背面加工も行うので複雑形状も1チャック加工が可能というものです。
当時、どの工作機械メーカーも「そんな加工機はできない!」という代物でした。私たちには、このコンセプトを実現できれば、必ず世界一になれるという強く高い志がありました。
仕様を決めるに当たっては、その年に開かれた国際工作機械見本市から業界の情報を集めました。個々の要素技術が現在どこまで進んでいるのか、徹底的に調査しました。設定する目標値は、これらをはるかに上回る必要があったのです。
モデル機の提示が、工作機械メーカーの度肝を抜く
複合加工機の1号機は、内視鏡の先端部品を段取りゼロの一発加工を狙って1999(平成11)年に立ち上げられました。1号機はオリンパステクノロジーフェア向けのマイクロファクトリー(小型工場)用モデル機でもありました。これは大きな反響を呼び、工作機械メーカーからも見学者が数多く来場しました。
また学会でも発表し、工作機械メーカーの度肝を抜きました。「工作機械メーカーではないオリンパスが、ここまでやるのか」というインパクトが工作機械業界に走ったのです。
ただし課題もありました。コンセプトは画期的なものですが、小型化を追求して大きさにこだわるあまりマシン剛性の課題があり、製造工場である会津オリンパスで加工検討しましたが、高精度加工は安定してできませんでした。しかし、「いつかきっと"もの"になる」という予感は心にしっかりと刻まれていました。
"ものづくり"の意地がドリームマシンを実現する
内視鏡や処置具等、微細な部品の高精度な組み立て技術では世界でトップクラスであると掲げるオリンパス内視鏡の製造工場(会津オリンパス)は、生産技術本部が提案した1号機の課題で、おずおずと引き下がるような姿勢は持ち合わせていませんでした。何としても「ドリームマシン」を立ち上げ、製造面でも競合他社を引き離して圧倒的に有利な立場を築き上げようとする強い意志が培われていました。
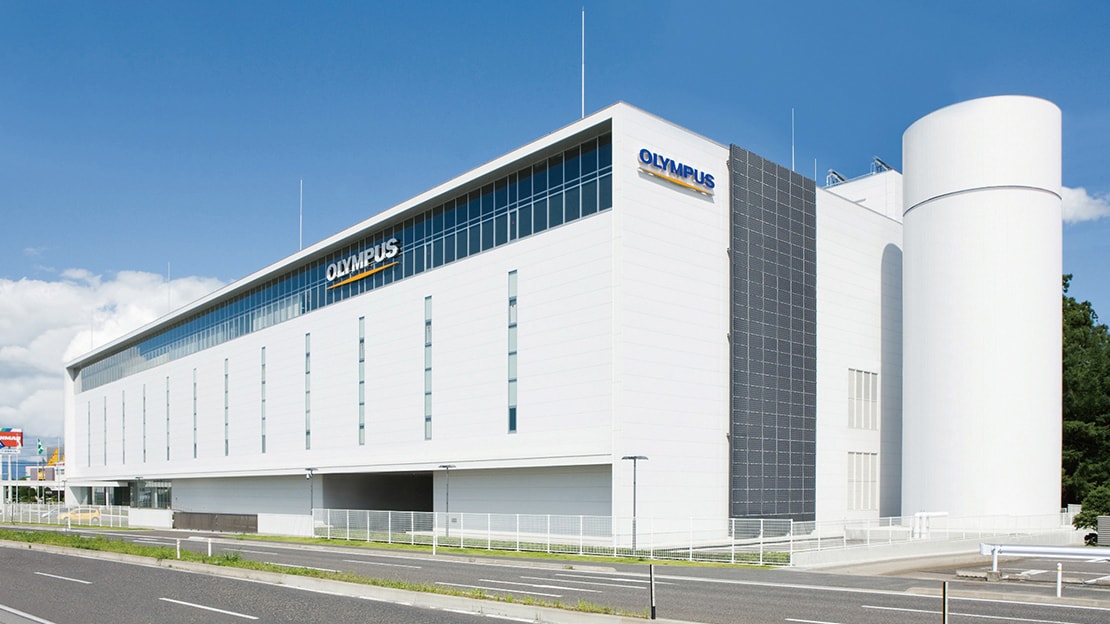
会津オリンパス
そこで、1号機の課題をすべて洗い出す作業を行い、コンセプトはそのままとし、設備設計技術者とともに2号機の設計に取りかかりました。このシステム開発には、医療技術開発部も取り組みました。
2号機では、ツール交換スピードを1号機の目標よりさらに速め、マシンを制御するソフトウエアや、1個加工を実現するためのCAM情報やツール情報に関連した情報システム面も強化して、加工スピードの向上を実現しました。
さらに、1号機で最大の課題となっていたマシンの剛性不足に対しては、単に剛性アップの設計を行うだけでなく、加工精度に直結する加工機の構成ユニットのひとつひとつの精度を徹底的に追求。立ち上げメンバー自らが、平面度の仕上げ作業に用いる「仕上げ砥石(といし)」を手に持ち、額に汗しながら鋳物部品の仕上げ作業に取り組んで、粘り強く丁寧に精度を追求しました。
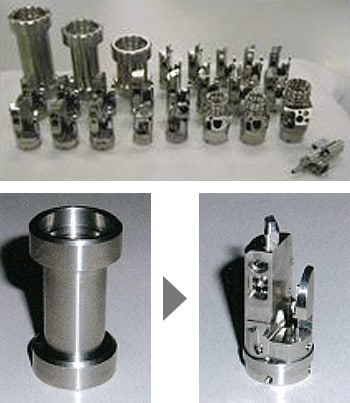
内視鏡の先端部品。段取りゼロの一発加工が行われる。
このように、複合加工機は、内視鏡の複雑形状部品の生産に活用できるレベルとなり、現在では会津オリンパスに数多く導入されています。工場を訪れた関係者たちは、この機械の前で必ず立ち止まり「ものづくりメーカーとしてこれが理想だ」と絶賛します。
オリンパスでは金属加工機だけでなく、レンズ加工機にもこの取組みが生かされています。レンズ加工の全工程を自動一貫生産する加工機がそれです。今後も複合加工機の成功に甘んじることなく、次世代の「ドリームマシン」に向け、検討を進めています。夢の追求に終わりはありません。